RA Power Solutions undertakes the Grinding of Crankshaft of High Capacity Engines used in Shipping companies, Power plants, and in various other sectors. The company has experience of more than forty years in undertaking successful repair of Crankshafts and major components. As we are aware Crankshaft is the heart of the engine and is the most expensive part with limited availability of particular make and model.
Our expertise lies in the repair of crankshafts that meets with a serious accident like a Seizure of a bearing. It is generally observed that due to rubbing of the bearing steel surface with the CR Pin diameter, excessive heat is generated. Thus there is an increase in Hardness. Every manufacturer specifies the maximum limit of Hardness.
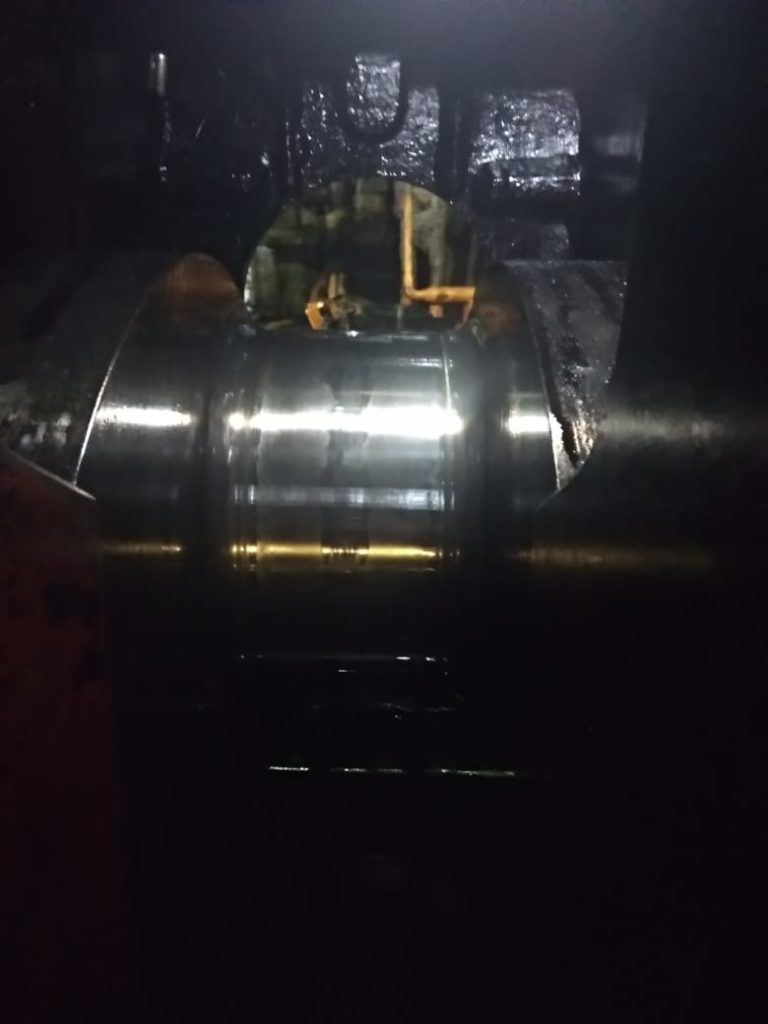
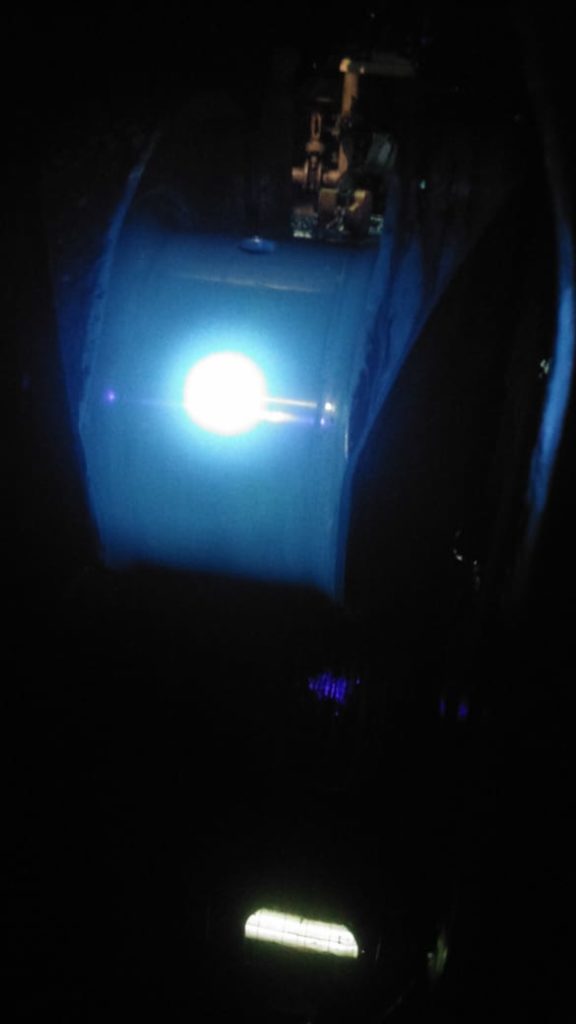
In the case of Mirrlees Blackstone K and KV, major series of engines, the normal hardness at the time of manufacturing of the crankshaft is between 21.5 to 26 on HRC Scale (241 to 268 on the HB scale). It is obvious that after the seizure of the bearing, the hardness increases even to the level of 45 to 50 HRC.
The Mirrlees Blackstone allows the higher hardness under a deviation maximum of up to 32 HRC against the standard of a maximum of 26 HRC. In normal situations as per the manufacturer, the crankshaft stands rejected as it has far higher Hardness than the stipulated in the manual.
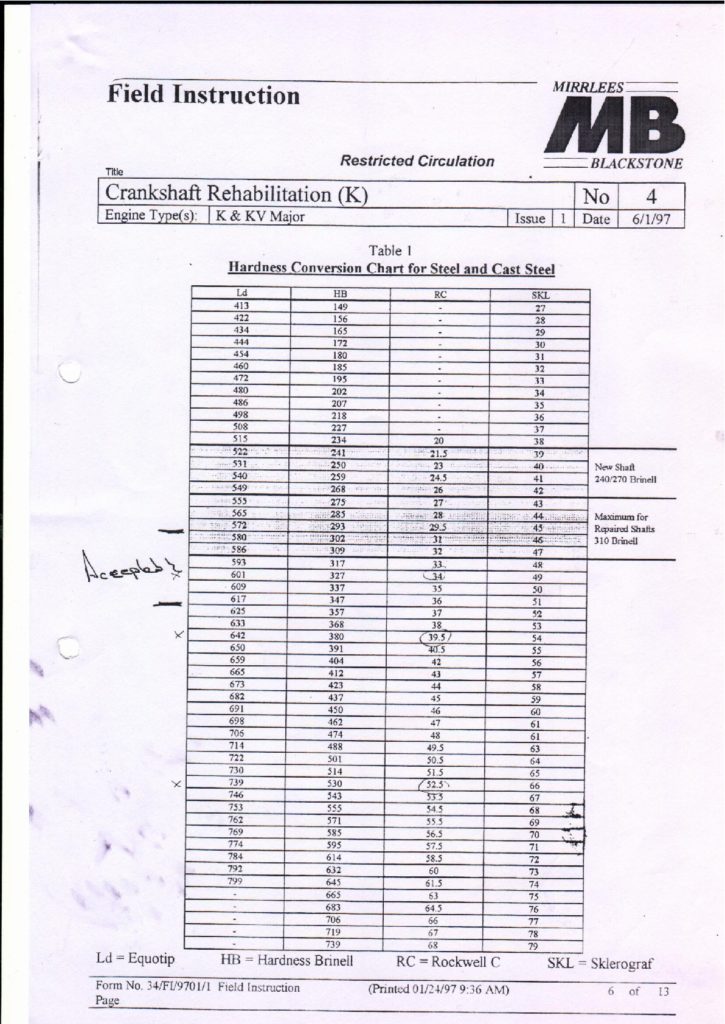
RA Power took the following action to save the Crankshaft.
- The Hardness was taken on various spots, not having a gap of more than 15 mm.
- Hardness was recorded and a maximum hardness of 50 HRC was observed.
- Since bearing line marks, taper, and ovality on the crank pin were observed, the grinding was undertaken and CR Pin dia was reduced by 3.5 mm approx.
- The Hardness was reduced and the maximum Hardness of 42 HRC was observed in a few spots. Although the 42 HRC Hardness was on the higher side than the maximum limit of 32 HRC specified by the manufacturer. The Crankshaft was accepted under deviation due to the following reasons:
- The higher Hardness was observed in a scattered pattern.
- The higher hardness was away from the Lubricating Oil Hole and radius fillet of the CR Pin which are considered to be critical Zone.
The versatility of RA Power Solutions crankshaft grinders caters to a wide range of marine and industrial crankshafts, irrespective of their size and design.
The Crankshaft was accepted and his performance is observed as satisfactory from last more than three and half years. The saving of the Crankshaft from rejection was possible only due to the Experience RA Power Solutions has of successful repair of more than ten thousand crankshafts.
RA Power Solutions undertakes Crankshaft Repair, Crankshaft Grinding and offers Onsite Crankshaft Machines to repair companies. We are a leading provider of crankshaft grinding and repair services, specializing in utilizing state-of-the-art crankshaft grinders.
With our state-of-the-art crankshaft grinders and highly skilled technicians, we can accurately recondition damaged or worn-out crankshafts to the original manufacturer’s specifications. By using advanced techniques and precision machinery, RA Power Solutions ensures that the repaired crankshafts regain their perfect alignment, surface finish, and dimensional integrity. Whether it’s a large marine engine or a compact generator, their expertise and commitment to quality make them a reliable choice for any crankshaft-related concerns.
With the use of RA Power Solutions crankshaft grinders, a significant decrease in downtime and repair costs can be achieved, allowing businesses to maintain productivity and efficiency.
Note: The writer of this article is Mr. Raj Shahani, Managing Director of RA Power Solutions Pvt Ltd.
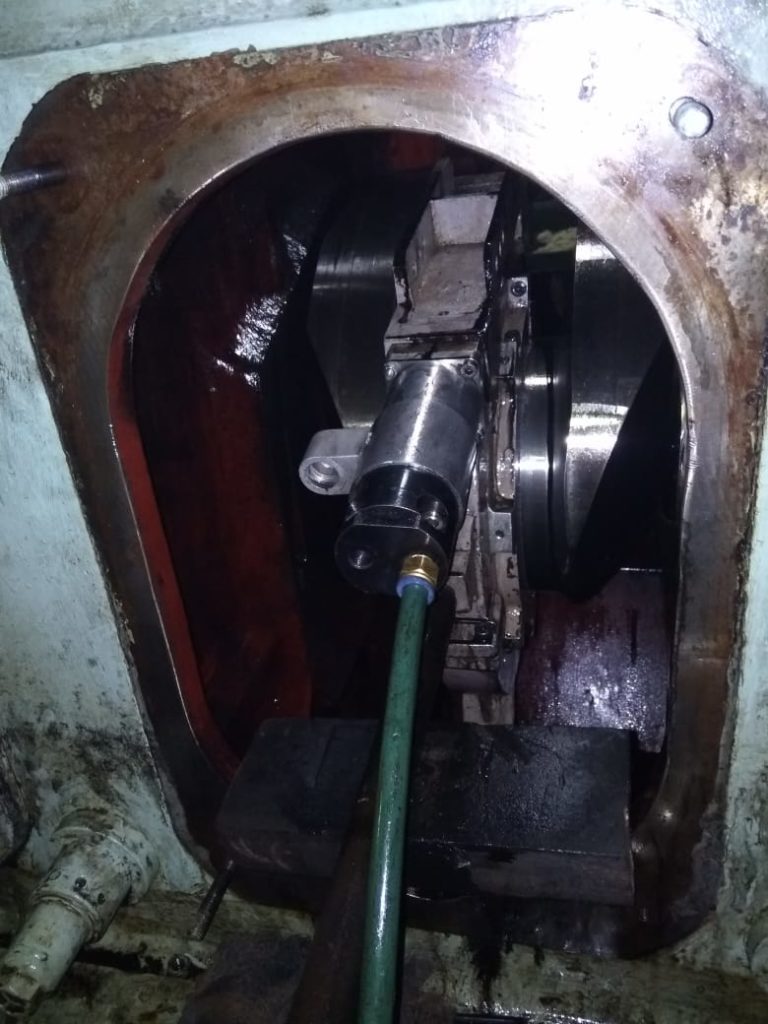
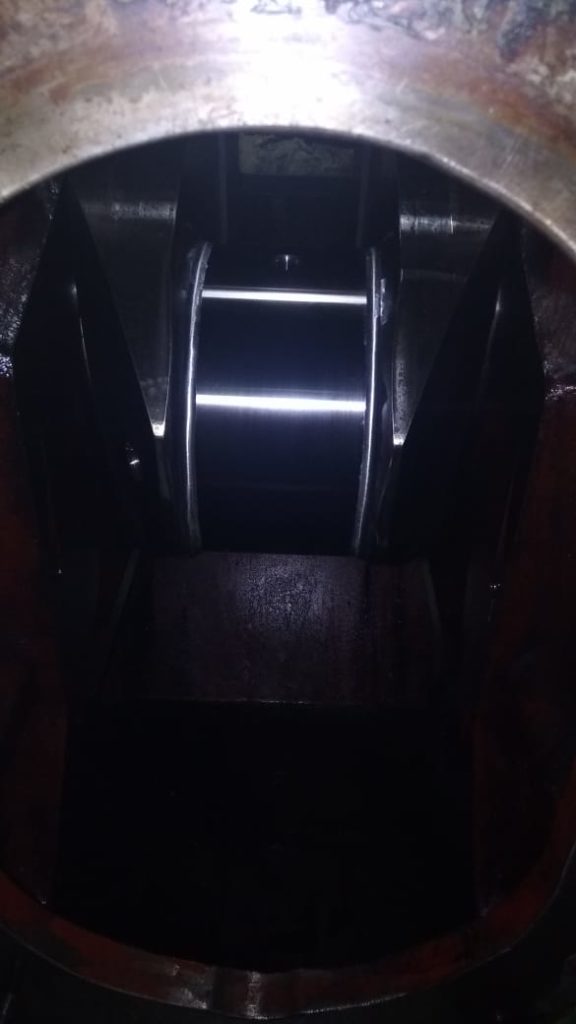
For more details on in situ crankshaft grinding and repair, crankshaft grinders, crankshaft grinding repair services, or crankshaft machining contact today by email us at rajshahani@rapowersolutions.com, or info@rapowersolutions.com, or call us at +91 9582647131 or +91 9810012383.