RA Power Solutions was approached by a leading Fertilizer producing company based in north India regarding the requirement of onsite grinding and polishing of compressor crankshaft.
The company has five high-capacity CO2 compressors which have been imported from a leading company based in Europe.
Our team consisting of three technicians along with onsite crankshaft grinding equipment was deputed to the site and following was observed:
Details of CO2 Compressor Crankshaft:
S. NO | Crankshaft Details | |
1 | Engine Make/ Model | CO2 COMPRESSOR |
2 | Crankpin Diameter Standard | 317.30 MM |
3 | Crankpin Bearing Width | 210.00 MM |
4 | Main Journal diameter | 330 mm & 317.30 mm |
5 | Main Journal Width | 370 mm & 225 mm |
6 | Place of execution of crankshaft repair | Fertilizers & Chemicals Plant in India |
- On dimensional inspection of crankpin it was observed that crankpin nos. 02 developed excessive ovality. It also had deep line marks due to the failure of bearings which are of babbitt white metal type.
- All the remaining crankpins were inspected and rough surfaces including bearing line marks were observed.
- The main journal having a standard diameter of 330 mm also had a rough surface and required polishing.
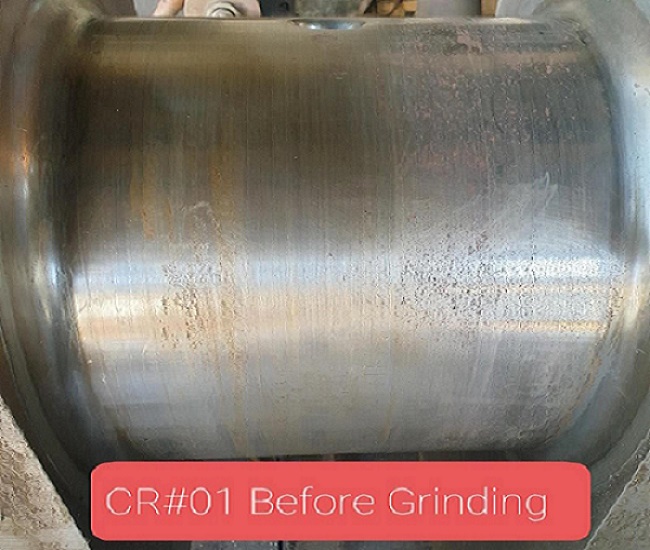
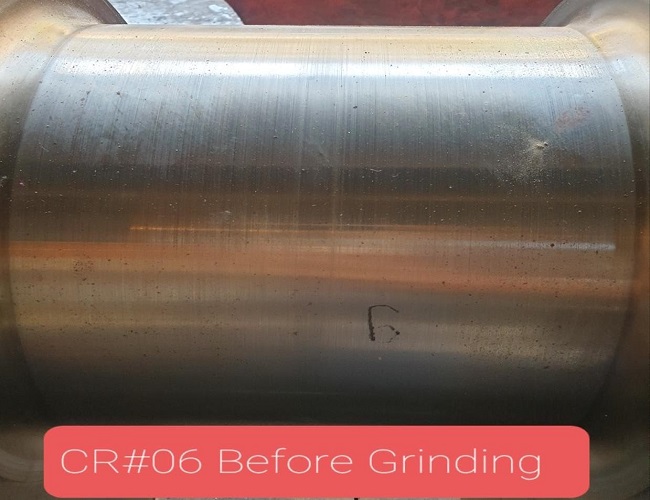
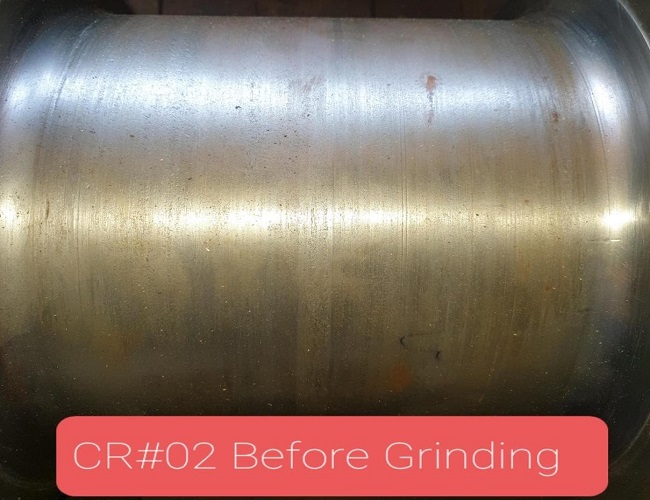
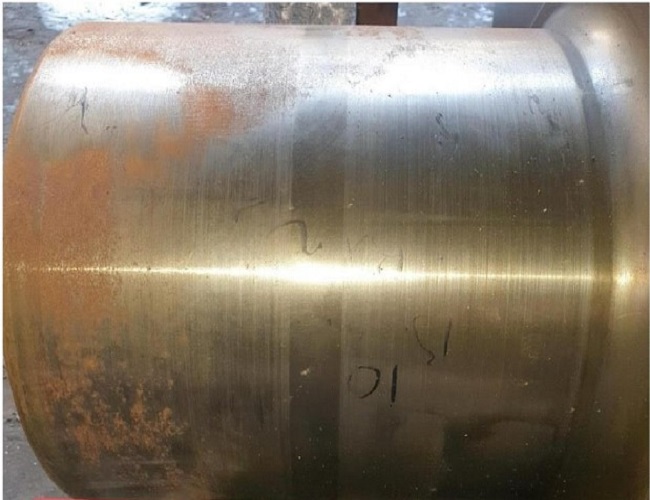
Action taken by RA Power Solutions
Considering the fact that the main journal having a diameter of 330 mm having a rough surface and bearing line marks it was decided to remove the crankshaft from the compressor.
RA Power Solutions technicians submitted a drawing of V-Block which were manufactured in the factory for placement of crankshaft.
The grinding of crankpin no. 02 was undertaken and the final dimensions were maintained between 315.58 mm to 315.60 mm. The ovality of only 0.02 mm was observed.
All the remaining 05 crankpins were polished, removing the line marks and improving the surface finish. The surface finish after polishing was observed at less than 15 RA value.
All the main journals were also polished onsite removing the ovality to some extent and improving the surface finish again to less than 15 RA value.
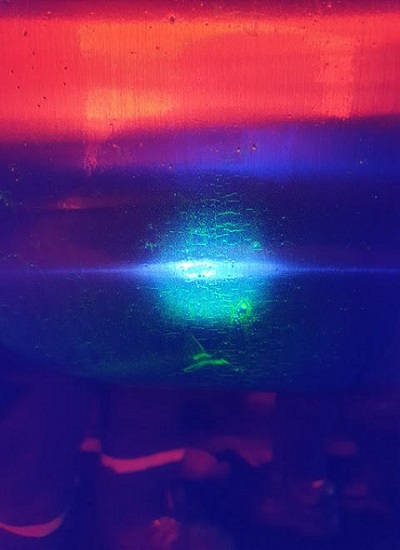
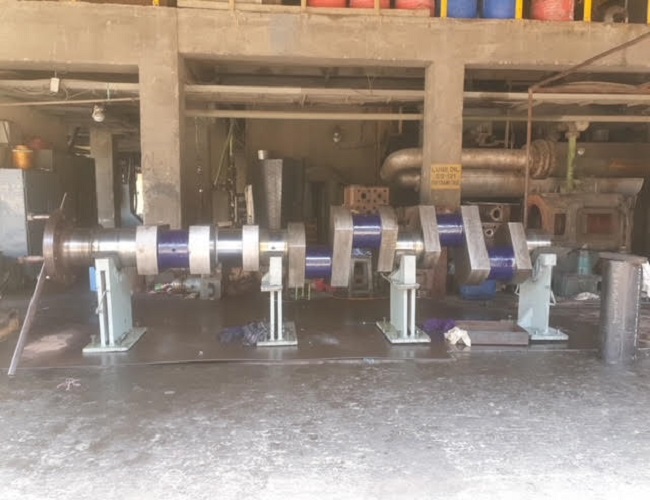
Advantage of getting the crankshaft grinding/ Polishing done by RA Power Solutions
- RA Power Solutions is the only company in India having experience of forty-three years in crankshaft repair.
- We have ready availability of equipment up to 700 mm diameter. The equipment is portable and lightweight and can be taken to any site all over the world as accompanied baggage. The modification in the onsite crankshaft grinding and polishing equipment is possible as per the site requirement.
- In this case since the main journal diameter was to be polished the V-Block was designed and fabricated onsite.
- RA Power Solutions as a protocol undertakes all the checks prior to grinding and polishing like cracks by MPI, Hardness test, deflection, etc.
- We also manufacture babbitt white metal bearings and do rebabbitting of old bearing up to 1500 mm diameter.
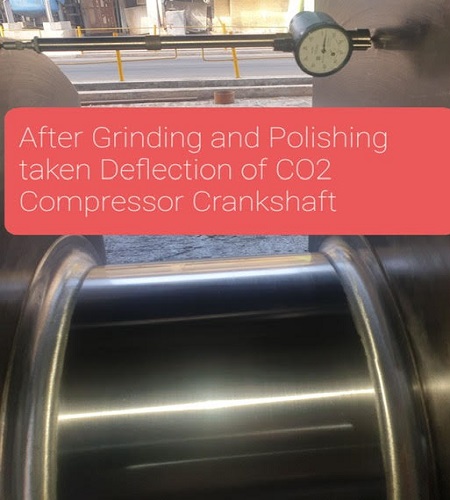
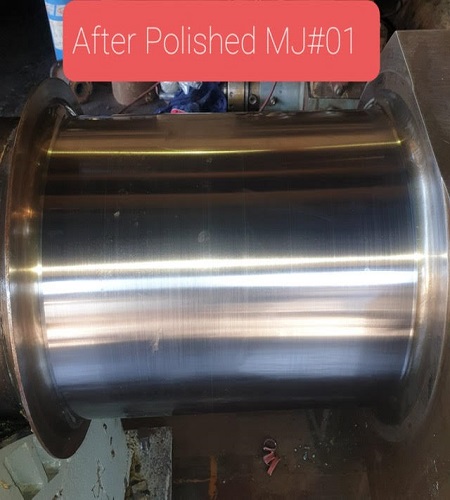
For more information on crankshaft grinding services, insitu crankshaft grinding and polishing, onsite crankshaft repair, or crankshaft polishing services email us at rajshahani@rapowersolutions.com, info@rapowersolutions.com Call at +91 9582647131,+91 9810012383.